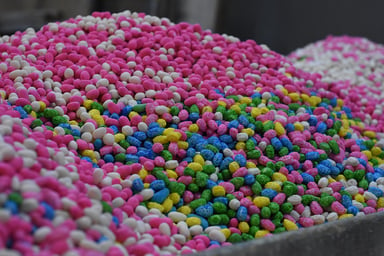
Catalytic Products International (CPI) has worked with a variety of confectioners to develop proven techniques to eliminate volatile organic compound (VOC) emissions from the panning / polishing and kitchen kettle operations for confectioners.
Coating edible products such as candy and chocolates often utilizes a panning / polishing process in which the edible product is coated with a confectioners glaze (a shellac/alcohol solution) as it tumbles in a revolving drum. Exhaust of the panning process will contain particulates including; sugars, starches, and other food grade ingredients. As drying air is introduced to the pan in order to evaporate the alcohol, significant emissions of VOCs such as Ethyl Alcohol, Ethyl Acetate, and Acetone, are exhausted into the air handling system and released into the environment.
Thermal or Catalytic Oxidization are the most widely accepted control technologies available to control the VOC emissions from the candy manufacturing process.
Catalytic Oxidizer
Catalytic treatment of VOC's and other air pollutants works by reacting the harmful air pollutants over a specially designed catalyst where VOC's are converted to CO2, water vapor (H2O), and usable heat. These harmless byproducts are passed through a heat exchanger where the gas streams energy is transferred to the incoming exhaust.
CPI installed a Catalytic Oxidizer (CatOx) at a Midwest USA candy manufacturer for the abatement of Volatile Organic Compounds (VOCs), from three (3) separate panning systems. The 5,000 SCFM Catalytic Oxidizer controlled the VOC emissions from the application of an alcohol-based confectioners glaze in one of three separate polishing pans. The CatOx includes a floating plate primary heat exchanger which met the operational requirements and provides lower operating costs for the customer. The Catalytic Oxidizer will destroy VOC emissions from the process with 95% destruction efficiency (DRE) and 75% thermal efficiency.
Each CPI Catalytic Oxidizer utilizes a high velocity mixing chamber at the burner, which forces flame impingement and turbulence to occur, providing excellent mixing of the air stream. This is a critical design element of an effective catalytic oxidizer. By designing for the highest mixing, the CPI CatOx system delivers high temperature uniformity before the catalyst bed. Temperature uniformity ensures that 100% of the catalyst is efficiently oxidizing the VOC’s.
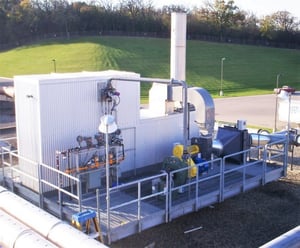
CPI worked closely with the customer to minimize the downtime associated with the removal of the old oxidizer and installation of the new catalytic oxidizer on the roof. Since this was a replacement of an existing oxidizer, CPI could utilize the existing VOC collection ductwork.
CPI provided on-site and in-office support to ensure coordination with the customer’s preferred contractors to ensure compliance with the provided bid specifications. CPI was able to complete a good portion of the installation activities before the new unit arrived on site for final assembly. This approach guaranteed that entire system was installed correctly, and the facility was back up and producing product with minimal downtime.
In another example, CPI installed a 12,000 SCFM Catalytic Oxidizer (CatOx) to control emissions from chocolate polishing and panning rooms. This system included a turnkey installation, with floor sweeps added to each room to evacuate the VOCs.
Regenerative Thermal Oxidizer (RTO)
Thermal treatment of VOC’s are also an effective technology for candy making operations. A Regenerative Thermal Oxidizer (RTO) offers high thermal efficiency due to the high thermal energy recovery of the heat exchanger media. The general operation of an RTO consists of passing process exhaust air (with VOC’s) through a heat exchange media where it is pre-heated. This pre-heated air enters a combustion chamber where it is heated to the setpoint temperature where oxidization of the VOC’s is completed. Hot treated clean air is cooled as it passes through the heat exchange media, which absorbs the heat to used during the pre-heat cycle.
Since 1969 CPI has been providing industry leading manufacturers with solutions to their air pollution control needs.
Today, CPI partners with its customers as a trusted resource in resolving the most complex air pollution and energy conservation problems. We provide our customers with innovative and cost-conscious solutions to their most complex VOC, NOx, and Odor pollution challenges. Our equipment is also at work meeting energy conservation strategies and minimizing greenhouse gas (GHG) emissions