Catalytic Products International (CPI) recently installed a 10,000 SCFM Regenerative Thermal Oxidizer (RTO) at a Southwestern Bioenergy facility for the abatement of Methane and Volatile Organic Compounds (VOCs) from an Anerobic Digestor used to convert dairy manure into pipeline quality, high BTU renewable natural gas (RNG).
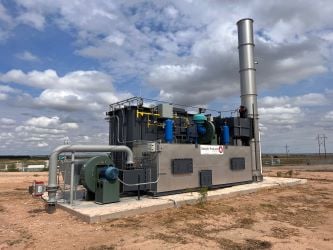
Anaerobic digestion is a series of biological processes in which microorganisms break down biodegradable material- such as manure- in the absence of oxygen. As the bacteria “work,” they generate biogas. The biogas that is generated is made mostly of methane and is combusted to generate electricity and heat or can be processed into renewable natural gas (RNG) and transportation fuels.
Some types of organic matter break down more easily than others. Generally, the more “digestible” the organic matter is, the more biogas can be produced. Co-digestion occurs when anaerobic digestion is used to break down multiple types of organic waste in one anaerobic digester. Organic wastes that can be used in co-digestion with manure include restaurant or cafeteria food wastes; food processing wastes or byproducts; fats, oil and grease from restaurant grease traps; energy crops; and crop residues. Co-digestion can increase biogas production from low-yielding or difficult-to-digest organic waste.
Biogas production is best suited for farms that collect manure:
- As a liquid, slurry or semi-solid;
- At a single point (a lagoon, pit, pond, tank or other similar structure);
- Every day or every other day;
- Free of large amounts of bedding or other materials (e.g., rocks, stones, straw or sand), which can clog the pipes of the digester and hinder operation.
Common anaerobic digestor designs include:
- Covered Lagoon: In a covered anaerobic lagoon design, methane is recovered and piped to the combustion device from a lagoon with a flexible cover. Some systems use a single cell for combined digestion and storage.
- Plug Flow: Plug flow digesters are primarily used at dairy operations that collect manure by scraping. Mixed plug flow systems have been used at a wider variety of operations because they can tolerate a broader range of solids concentrations.
- Complete Mix: Complete mix digesters are designed with an enclosed, heated tank with a mechanical, hydraulic or gas mixing system. Complete mix digesters work best when there is some dilution of the excreted manure with water (e.g., milking center wastewater).
- Batch Digester: A batch digester is the simplest form of digestion, where manure is added to the reactor at the beginning of the process in a batch and the reactor remains closed for the duration of the process.
- Induced Blanket Reactors: Induced Blanket Reactors are digesters in which a blanket of sludge develops and retains anaerobic bacteria, providing a bacteria-rich environment through which the feedstock must pass.
- Fixed Film Digesters: Fixed film digesters contain plastic media (e.g., pellets) on which bacteria attach and grow, instead of relying solely on suspended bacteria to break down the digester feedstock.
A Regenerative Thermal Oxidizer was selected for this lagoon-type anaerobic digester due to the CO2 and Methane concentrations that would result in high auxiliary fuel consumption for a thermal combustor. The RTO will reduce the auxiliary fuel operating costs of the oxidizer to zero (auxiliary fuel is needed for start-up and when the unit is idling without the tail gas being processed) and provide a long lasting, high uptime air pollution control system.
The TRITON 10.95 RTO with a hot gas by-pass will control the waste stream or tail gas emissions from the high BTU gas purification system. The RTO will successfully destroy the Methane and VOCs from the purification system with a +98.5% destruction rate efficiency (DRE) and a thermal efficiency of 95%.
Thermal treatment of VOCs and other air pollutants works by a simple reaction of the harmful hydrocarbon-based air pollutants with oxygen and heat. In this environment, the VOCs are oxidized to form harmless inert by-products like CO2, water vapor (H2O), and usable heat. These harmless by-products are released to the atmosphere or used within primary or secondary energy recovery techniques to further lower the operational costs.
CPI Regenerative Thermal Oxidizers (RTOs) are engineered to provide exceptional performance and reliability. During operation of the standard two chamber RTO, the VOCs are directed into one of the system’s regenerators, an internally insulated vessel containing specialized ceramic media which allows thermal rate efficiencies up to 97%. The contaminated gases are passed through the first regenerator where energy is transferred from the ceramic media to the gas in order to elevate the temperature. This elevated temperature approaches the ignition level for most solvents and is then directed from the ceramic bed into the combustion chamber. As the stream exits the ceramic bed and travels through the internally lined combustion chamber, minimal heat is added to ensure a proper oxidation temperature and a designed dwell time is maintained providing destruction of the VOCS at greater than 98% efficiency. The resultant clean, oxidized gases are directed to the second regenerator to absorb the heat energy before being released to the atmosphere.
Catalytic Products International (CPI) worked closely with the customer to provide the engineering, design, supply, and startup of the RTO. The RTO was delivered pre-piped and wired and CPI provided engineering support and on-site supervision to ensure the entire system was installed correctly. CPI also designed and supplied the exhaust stack, booster fan, and pre-fabricated, weather-proof, insulated control house.
The process gas contains a high concentration of CO2 mixed with water vapor, which may form carbonic acid. To prevent corrosion the RTO is constructed of stainless steel for the wetted surfaces of the RTO and for any other components that will come in contact with the process gas.
Renewable Natural Gas (RNG) from Agricultural-Based AD/Biogas Systems is a focus of several Federal and State public policy initiatives. More information can be found here from the US EPA AgSTAR program, which is a collaborative program sponsored by the EPA and USDA that promotes the use of biogas recovery systems to reduce methane emissions from livestock waste.
CPI has been “Enabling Clean Production Since 1969” and continues as a leading supplier of air pollution control equipment. CPI is at the forefront in providing industries including the bioenergy industry with solutions to their air pollution control needs.