“What just happened?” – a phase all too often heard when equipment is not working the way it is supposed to. A glitch in the system? Power surge? Or maybe a small modification in your production was made. Could that have caused the current problem? You're responsible for getting the equipment operational as fast as possible.
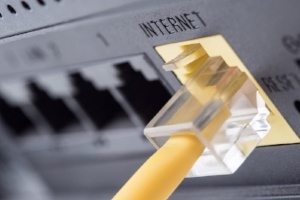
While local general service technicians (ex: HVAC, plumbing, electrical) can be onsite rather quickly as a first responder in an emergency, an expert equipment maintenance technician for your custom equipment can take more time to get to your site.
The first step in communicating with your equipment manufacturer, or air pollution control equipment expert is a phone call with the service department who can provide some basic troubleshooting. A technician can walk you through troubleshooting and/or fixing failed parts and pieces. They can also provide you with insight to system sequencing and operational control strategies. Identifying mechanical issues such as pressure switch failures, faulty thermocouples or gas control valves is one thing.
Sometimes, it can be a bit more complicated. Modern day machinery, just like automobiles, are run by complex control systems. Depending on the circumstance, these control systems can require parameter changes to allow for production changes. Having an expert service technician come out on site is possible, however this is not always practical. One solution to mitigate downtime and costly service calls, is to enable Remote Access either through a dedicated connection, or via a cellular modem. CPI provides all of our equipment with the hardware necessary for remote connection, it is up to the end user to determine if enabling this connection is a benefit for their business.
If your oxidizer system is more than five years old, we recommend a review of your current control strategy. Replacing obsolete components can reduce unexpected maintenance downtime and technology advancements can cut down on expensive on-site service calls.