This month, CPI would like to dig deep into the guts of the Regenerative Thermal Oxidizer (RTO) to share an educated understanding of RTO ceramic heat exchange media. In all RTO applications, the selection of the type of media required to best suit your needs is an important decision when buying an RTO, but it could also be an area for improvement in equipment rebuilds. To get started, let’s review the basic types of RTO ceramic heat exchange media:
Structured RTO Ceramic Heat Exchange Media
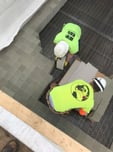
A structured heat exchange media packs a high density of ceramic into a small area while offering a lower pressure drop. A typical example of this is Multi-Layer Media (MLM). MLM is also the most cost effective style of media in RTO applications.
Monolith RTO Ceramic Heat Exchange Media
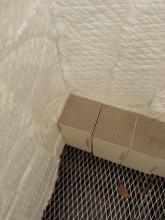
This an extruded block that offers the most open area and the lowest pressure drop. This style of RTO ceramic media also has flexibility with cell density, wall thickness, and materials of construction that allows for custom heat recovery designs that can be optimized for difficult applications that may include particulate, alkali, or ceramic fluxes.
Random RTO Ceramic Heat Exchange Media
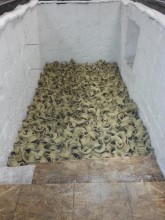
This ceramic RTO media is typically offered in the form of saddles, rings, balls, dog bones, or other shapes. This provides a reliable heat exchange at a higher pressure drop than monolith or structured media.
By design, RTO ceramic heat exchange media should be relatively care-free. Most RTO ceramic heat exchange media is designed to last the life of the RTO with the absence of some process containment such as condensable materials like phenolic resin, silicones, ceramic fluxes, or other inorganic materials. With that being the case, CPI would like to share some characteristics that may guide maintenance teams to review the performance of their ceramic heat exchange media. Loss of air flow capacity through the RTO, as well as increased pressure drop across the RTO ceramic heat exchanger beds, are indications that the RTO media may be performing Insufficiently.
Maintenance Recommendations:
Below are typical RTO media replacement applications and some issues that have been identified and overcome.
Settling of ceramic heat exchange media: Random media has a tendency to settle after operation of the system. If the bed is completely constructed of random media, settling is normally not an issue, as long as the settling does not create areas where flow is high enough to fluidize the ceramic media. If the design required use of random media to fill in the gaps along the wall, settling could cause issues with the structured block or monolith tipping over.
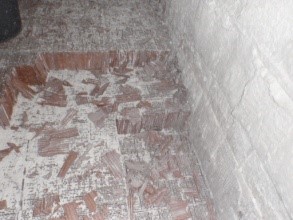
Plugging of ceramic heat exchanger media: Applications that include silohexanes or other volatile organic compounds (VOCs) with silicone attached have a potential of forming silica dioxide (SiO2) during the combustion process. The SiO2 is inorganic and will eventually plug the ceramic heat exchanger media. Other potential plugging items within RTOs are any inorganic substances that are part of the VOC stream being sent to the oxidizer.
Plugging of the cold face support: Applications that include condensable solvents (long carbon chain VOCs) like magie oils, phenolic resins, or paint may start to cover the cold face support of the ceramic heat exchange media. Depending on the design of the heat exchanger, these solvents also have a tendency to condense and eventually plug the lower level of the ceramic heat exchange media as well.
Chemical attack of the ceramic media: Applications that include alkali, heavy metals, fluorine, or other fluxes can cause softening, cracking, and physical degradation of the media beds.
Burner exposure: Poor oxidizer design, improper burner setup, or operation in a low O2 environment could allow for coating the media in fuel in oil fired applications or an extended flame in other applications. The flame temperature is higher than the melting temperature of the ceramic, which will cause problems.
CPI would like to thank you for your interest in proper maintenance of the RTO ceramic media. As always, in times of faulty operation, please feel free to contact CPI’s Service Team for your trouble shooting and service needs. Please join us next month as we explore the maintenance requirements of a RTO’s poppet valves.