Air pollution control is a topic that is incredibly relevant in the chemical manufacturing industry as restrictions on emissions are becoming more and more stringent. We wanted to spotlight how CPI’s QUADRANT SR-Series Thermal Oxidizer can provide air pollution control solutions for this industry, but first, let’s look at the terminology and technology:
- VOCs: (Volatile Organic Compounds) are organic chemicals that have a high vapor pressure at ordinary room temperature. Their high vapor pressure results from a low boiling point, which causes large numbers of molecules to evaporate or sublimate fom the liquid or solid form of the compound and enter the surrounding air, a trait known as volatility. For example, formaldehyde, which evaporates from paint, has a boiling point of only –19° C (–2° F).
- HAP: Hazardous Air Pollutants.
- MACT: The Maximum Achievable Control Technology standard is a level of control that was introduced by Title III of the 1990 Clean Air Act Amendments. The purpose of these Amendments was to expedite the development of standards that would reduce hazardous air pollutant (HAP) emissions.
VOC and HAP emissions can be generated throughout the chemical manufacturing process, originating from sources such as process vents, storage tanks, and fugitive releases.
In order to meet MACT standards, a variety of air pollution control processes are available, including adsorption, biofiltration, condensation, thermal oxidation, UV light oxidation, and wet scrubbing, as well as combinations of these processes. Many of today's chemical processing facilities use thermal oxidation systems, but within this category of air pollution abatement devices, there are still more options: catalytic oxidation, regenerative thermal oxidation, thermal (recuperative) oxidation, and direct thermal oxidation.
A Thermal Oxidation Solution With the QUADRANT SR-Series
We worked with a chemical processing facility that needed to design and install a system which would exceed MACT requirements while remaining highly reliable and capable of handling a wide range of emission characteristics from their vent streams. We were able to address these needs through the installation of a QUADRANT SR-7,000 Thermal Oxidizer with a specially engineered primary heat exchanger with a shell and tube design.
A Thermal (recuperative) Oxidizer controls harmful air pollutants by combining them with oxygen and heat, converting VOCs into CO2 and water vapor. In this system, the byproducts were then released over the shell and tube heat exchanger, allowing for energy recovery.
Controlling this reaction in a recuperative thermal oxidizer can be a complicated process, especially since many emission points can cycle on and off at various times, and reactions that take place during the process can result in changing emission loadings. This particular application was additionally complicated by the inclusion of a regularly-changing variety of solvents, including hydro-carbons, aldehydes, esters, and acids, and by the facility’s desire to engineer a highly fuel efficient device. Since the solvent loading was constantly changing (from low to high), the Thermal (recuperative) Oxidizer had to be designed with a special heat exchanger that was capable of handling this wide range of emissions while providing the reliable uptime the facility needed.
The system needed to be able to process emissions from 5 different reactor vents totaling 7,000 standard cubic feet per minute (SCFM). The temperature of these vents varied slightly from ambient to 130° F, and the loading variations could range from about 1% LEL (lower explosive limit) to more than 25% LEL. While the facility’s environmental permit called for a minimum destruction rate efficiency of 99%, the goal was for this device to obtain a 99.9% efficiency rate.
CPI was able to meet these needs with a QUADRANT SR-7,000 Thermal Oxidizer. This oxidizer is designed to effectively process the necessary range of emissions and volumes without compromising the facility’s operation. The installed system also utilized a floating tube heat exchanger which was engineered to lower the fuel consumption at all times. By offering a completely stress free design, this heat exchanger proved beneficial in this demanding application. As a result, the system was able to meet the client’s expectations for both compliance and operating costs. The oxidizer has proven to be highly reliable, meeting the required uptime goals, and only requiring downtime for normal preventive maintenance tasks.
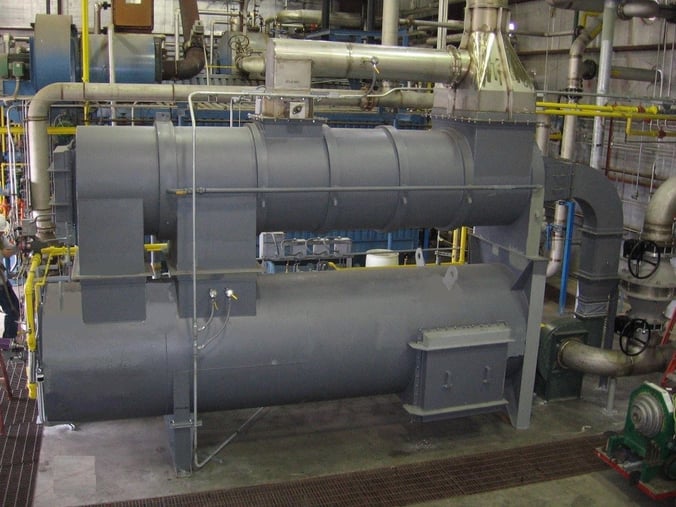
The QUADRANT family of thermal oxidizers is available in four different configurations. These systems are capable of treating emissions up to 50,000 SCFM and solvent concentrations exceeding 100% LEL. Special systems are also available to treat halogenated air streams. If you have any questions about how these systems can help you manage air pollution in your chemical processing facility, please contact us.
At Catalytic Products International, we work to make sure that our customers have the best solutions to their air pollution remediation needs and that they have the knowledge to continue to meet these needs as they grow and change. For more examples of how our expertise helps our clients find success, please read our Customer Testimonials.